Quick and Reliable Product Packaging Device Repair Service Services to Decrease Downtime
In the affordable landscape of manufacturing, the performance of product packaging operations pivots on the integrity of machinery. Quick and reliable fixing services are essential in alleviating downtime, which can cause significant operational troubles and monetary losses. Understanding the relevance of timely treatments and the function of expert service technicians can transform just how companies come close to repair and maintenance. Navigating the myriad choices available for repair work solutions can be challenging. What aspects should businesses take into consideration to ensure they are making the appropriate choice for their operational requirements?
Relevance of Timely Repair Works
Prompt fixings of product packaging equipments are crucial for maintaining operational effectiveness and decreasing downtime. In the busy setting of manufacturing and packaging, even minor malfunctions can cause considerable delays and productivity losses. Addressing issues without delay guarantees that devices operate at their optimum ability, consequently securing the flow of operations.
Additionally, routine and timely maintenance can avoid the acceleration of minor troubles right into major failures, which usually incur higher fixing expenses and longer downtimes. A proactive strategy to maker repair work not only preserves the honesty of the devices but additionally improves the overall reliability of the assembly line.
Furthermore, timely repairs add to the durability of packaging machinery. Makers that are serviced quickly are much less likely to experience extreme deterioration, allowing services to maximize their financial investments. This is especially crucial in industries where high-speed product packaging is important, as the requirement for constant performance is paramount.
Advantages of Reliable Solution Carriers
Trustworthy service companies play a critical function in making sure the smooth procedure of product packaging makers. Their know-how not just boosts the effectiveness of repair work however likewise adds significantly to the longevity of equipment.

Furthermore, a trustworthy company provides detailed support, including training and assistance for staff on machine operation and upkeep best practices. This not only encourages staff members yet likewise cultivates a culture of security and effectiveness within the organization. Overall, the advantages of involving trustworthy service carriers prolong beyond immediate repairs, favorably affecting the entire functional operations of product packaging processes.
Common Product Packaging Maker Issues
In the realm of product packaging operations, various concerns can jeopardize the efficiency and capability of makers. One prevalent trouble is mechanical failing, typically originating from deterioration or inadequate upkeep. Parts such as belts, gears, and electric motors might stop working, leading to failures that halt production. An additional common concern is misalignment, which can create jams and uneven product packaging, impacting item high quality and throughput.
Electric problems can likewise interfere with packaging procedures. Defective circuitry or malfunctioning sensing units may lead to irregular machine habits, creating delays and boosted functional costs. Additionally, software program problems can hinder the equipment's programs, causing functional inefficiencies.
Inconsistent product flow is another important concern. This can arise from variations in product size, weight, or shape, which may impact the maker's capability to manage things properly. Insufficient training of operators can exacerbate these problems, as untrained workers might not identify very early indications of malfunction or may misuse the equipment.
Dealing with these common packaging machine concerns without delay is essential to keeping efficiency and making sure a smooth operation. Regular inspections and aggressive upkeep can substantially reduce these problems, cultivating a reliable product packaging atmosphere.
Tips for Reducing Downtime
To minimize downtime in product packaging operations, carrying out a positive maintenance approach is vital. On a regular basis arranged upkeep checks can identify potential concerns before they rise, making sure devices run effectively. Establishing a routine that includes lubrication, calibration, and inspection of essential elements can significantly minimize the frequency of unexpected failures.
Training personnel to basics operate machinery appropriately and acknowledge very early caution indications of breakdown can also play an essential role. Encouraging operators with the understanding to do basic troubleshooting can stop small issues from triggering significant delays. Preserving an efficient supply of important spare components can accelerate fixings, as waiting for parts can lead to prolonged downtime.
Furthermore, recording equipment performance and maintenance tasks can help identify patterns and frequent troubles, permitting targeted interventions. Integrating sophisticated monitoring innovations can supply real-time information, making it possible for anticipating upkeep and minimizing the risk of sudden failings.
Lastly, fostering open communication between operators and upkeep groups ensures that any abnormalities are immediately Go Here reported and resolved. By taking these aggressive actions, businesses can boost functional effectiveness and substantially minimize downtime in packaging processes.
Choosing the Right Repair Service
Choosing the proper repair work service for packaging equipments is a critical choice that can dramatically impact operational efficiency. An appropriate provider guarantees that your equipment is fixed quickly, properly, and to the highest possible requirements. Begin by assessing the service provider's experience with your specific kind of product packaging equipment. A technician acquainted with your machinery can identify issues extra accurately and execute solutions extra quickly.
Following, consider the provider's track record. Looking for comments from other companies within your sector can offer understandings into dependability and top quality. Accreditations and collaborations with acknowledged tools manufacturers can likewise show a commitment to excellence.
In addition, evaluate their action time and schedule. A service supplier that can offer timely assistance decreases downtime and maintains production flow consistent. It's additionally essential to ask concerning service warranty and service assurances, which can mirror the self-confidence the service provider has in their work.

Conclusion
Finally, the value of reliable and fast packaging equipment repair service solutions can not be overstated, as they play a crucial duty in reducing downtime and making certain operational performance. By prioritizing prompt repairs and picking reliable read this article provider, organizations can efficiently resolve typical concerns and keep performance. Executing aggressive maintenance methods and buying staff training further improves the longevity of packaging equipment. Inevitably, a tactical strategy to repair services promotes an extra resilient production atmosphere.
Timely repairs of packaging devices are vital for keeping functional performance and decreasing downtime.In addition, prompt fixings contribute to the durability of packaging machinery. In general, the benefits of engaging reliable service providers expand beyond instant repair work, positively impacting the whole functional process of packaging processes.
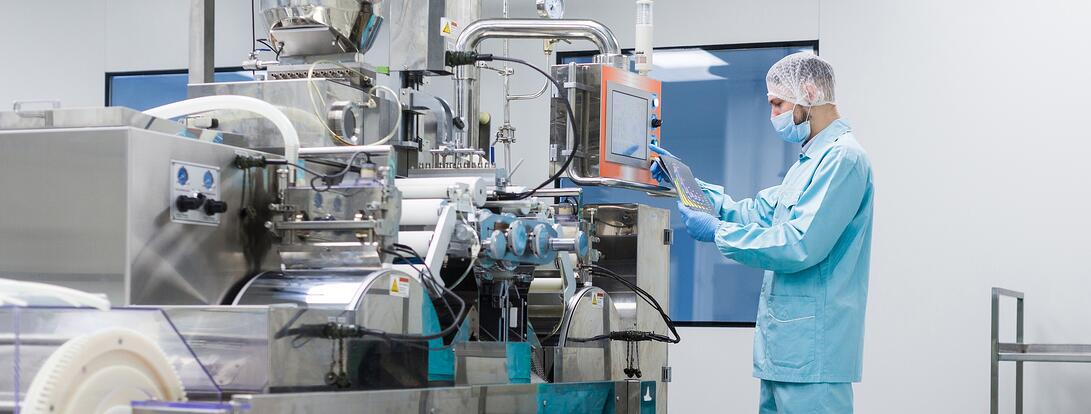
Comments on “Troubleshooting Your Equipment: When to Call for Packaging Machine Repair”